The injection molding process of a plastic product is usually divided into two stages: in the first stage, most of the plastic is fed into the mold, generally accounting for 90% to 99.9% of the entire product volume; in the second stage, the product is compacted, to obtain a product that shares the same structure and shape with the mold.
In the second stage, though only a smaller amount of molten plastic is fed into the cavity, it is very important for the surface finish, the aesthetic appearance, and the dimensions of the product. In most cases, the second stage of plastic injection molding is called pressure holding prcoess ,it involves two parameters, i.e., holding pressure and holding time.
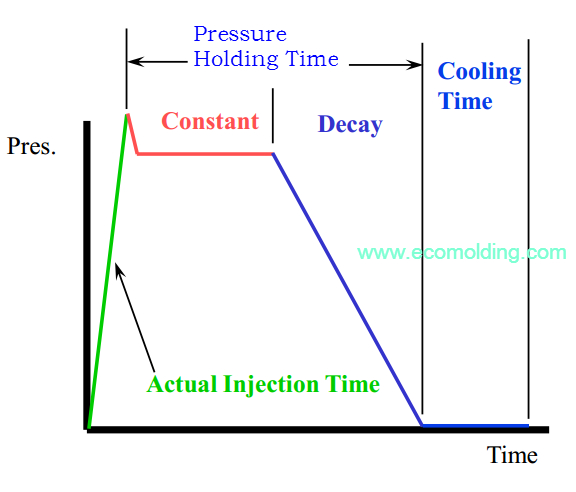
We now increase the factors from two to four:
- The method of transitioning from the first stage to the second stage;
- Process the product while keeping the gate sealed (frozen) or unsealed;
- Pressure holding time;
- Maintain proper pressure in the cavity.
Transition
We may say that it is the most critical part in the plastic injection molding process to properly control the transition from the first stage to the second stage, as it decides whether we are able to produce high quality products. And also, it is often the reason that a plastics processing plant is not able to produce two identical products on two different sets of equipment.
It is necessary to ensure that the first stage transitions to the second stage quickly and consistently. Therefore, understanding how an injection molding machine works is of critical importance to achieve the desired results. With regard to most products and proper process control, from end of the first stage to the pressure set point of the second stage, the time interval should be kept within 0.1 seconds.
Set Pressure Holding Time
Knowing whether you should keep the gate sealed or open is able to help set the duration of the second stage. If gate sealing time is required, a longer gate sealing time or a second gate sealing session is needed to maintain the intensity and stability of the process.
This does not necessarily require an increase in cycle time, as in most environments, balance can be achieved by reducing cooling or mold sealing time. If product performance can be better guaranteed with the gate unsealed, the gate should be cooled at half the time required.
A relevant approach: if the gate is not sealed during the process, the consistency of cycle duration becomes very critical for consistent products. If the cycle duration changes with the gate unsealed, the product will also change due to the different amounts of polymers in the cavity, which can be checked by weighing the product.
Set Holding Pressure
It is of critical importance to find the right holding pressure for compacting the product. The proper pressure for the second stage should be kept within the range of product parameters required to obtain a product with great CPK (Process Capability Index), and at the center of it. Since holding pressure is set under gate seal testing conditions, the correct compacting and holding pressure values for the second stage should also be identified through testing, which will thus be set as the central value within the range of product processing parameters.
First, check the stability of the first stage, and whether there is insufficient filling or product shrinkage after the first stage ends.
If the first stage is stable enough, then start to increase the holding pressure. From low to high, it may only require a pressure of 1000 to 2000psi for plastic materials. Check the product each time the holding pressure is raised; raise the holding pressure in small increments until the product quality is deemed to be the most acceptable. Produce a certain number of products that require preliminary quality test, then, label and put them away.
Now, continue to raise the holding pressure, until unacceptable flashing, ejector marks and mold adhesion issues appear during production. Lower the pressure to the maximum allowable value for processing, so as to achieve safe and efficient production.
The max. holding pressure formula as below:
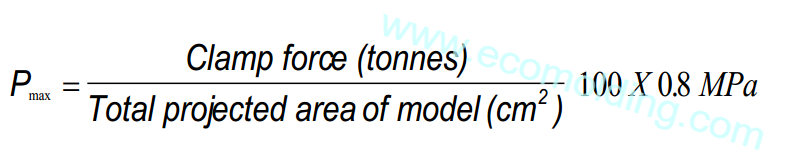