Influence of Injection Mold Cooling
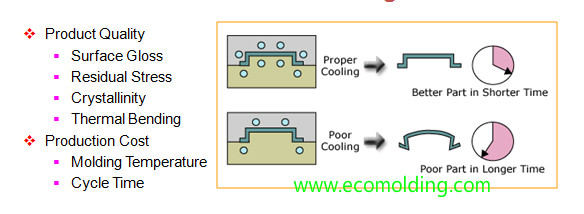
Influence on Product Quality
Surface Gloss: Many materials require a relatively high mold surface temperature to achieve a great surface gloss in production. If the cavity temperature is different between some areas and others, a different surface gloss will be seen on the finished product surface.
Residual Stress: Residual stress is the result of shear stress during resin filling or pressure holding. In addition to the stress caused by the flowing melt, residual stress is also produced when the various parts are cooled at different rates due to the different surface temperatures of the product. These residual stresses may be the cause of premature failure, warpage or distortion of the product during application. In order to reduce these stresses, uniform cooling is required.
Crystallinity: The crystallinity exhibited during the injection molding process of semi-crystalline materials is influenced by the cooling of the melt. The difference in crystallinity during product cooling affects the volumetric shrinkage, so it is therefore difficult to maintain the required dimensional tolerances. Significant changes in volumetric shrinkage in different areas are often a cause of product warpage.
Thermal Bending: If the temperatures of the upper and lower surfaces of the mold are different, once the product is ejected from the mold, the product will bend due to the different thermal shrinkage rates between the upper and lower surfaces.
Ejection Temperature: The temperature at which the product is ejected from the mold can be affected by many factors. The strength of the product must be large enough to resist warpage due to changes in volumetric shrinkage and residual stress, as well as local stresses imposed on the product by the ejector system. The ejection force is influenced by the geometry of the product, the surface gloss of the mold, and the filling of the cavity during resin filling and pressure holding.
Cycle Time: Mostly, the cycle time is the time it takes for the temperature of the product to drop to a safe ejection temperature. If the resin filling and pressure holding processes are optimized, the improvement of cooling
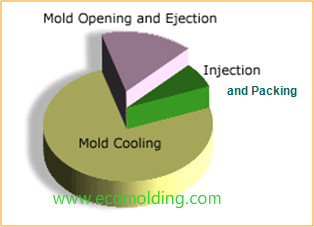
behavior can significantly reduce the cooling time. Since the cooling time typically accounts for 80% of the cycle time, reducing the cooling time is able to significantly reduce the cycle time and production cost.

Components of Injection Mold Cooling Systems
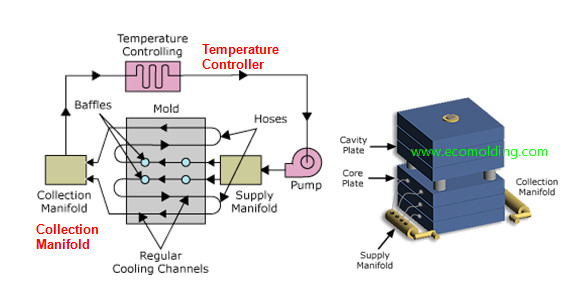
Types of Cooling System
Series Cooling
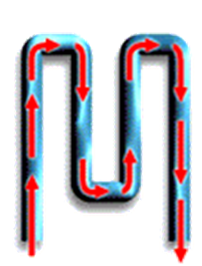
Pros:
– Even flow rate
– Even thermal distribution
Cons:
– High pressure drop
Parallel Cooling
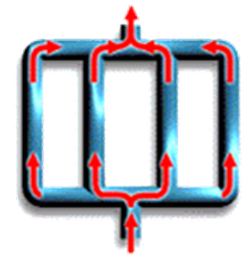
Pros:
– Suitable for areas around the washer
– High flow rate at low pressure
Cons:
– Different flow rates in each sub channel
– Poor cooling effect in each sub-channel
– Easy to produce dirt
Basic Forms of Injection Mold Cooling Systems
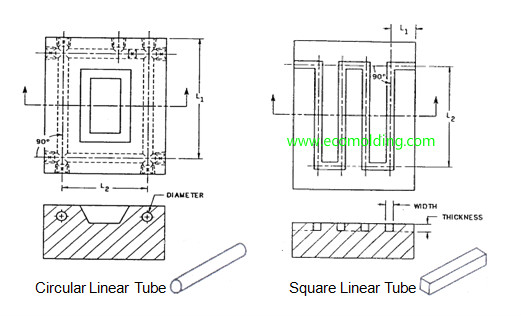

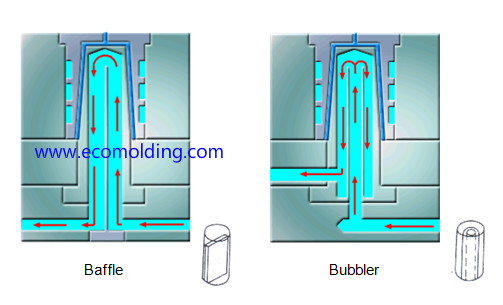
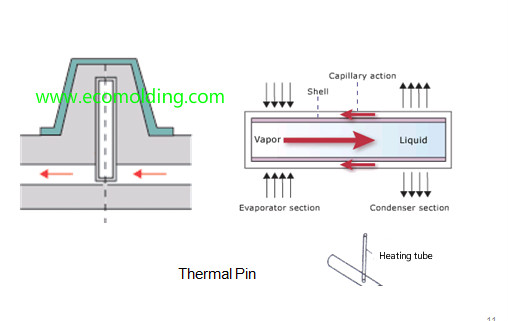
Objectives of Injection Mold Cooling Systems Design
The design of the cooling system is often limited by the geometry of the cavity, the parting surface, the slider and the ejector pin, so the design guidelines for the ideal distribution cannot be given rigidly.
The goal of the mold designer should be to take all the aspects into consideration, and design a proper cooling system that will:
Evenly cool the molded product
Reduce the molding cycle time
Ensure Uniform Cooling via Channel Layout
Close to hotter areas
Away from cooler areas
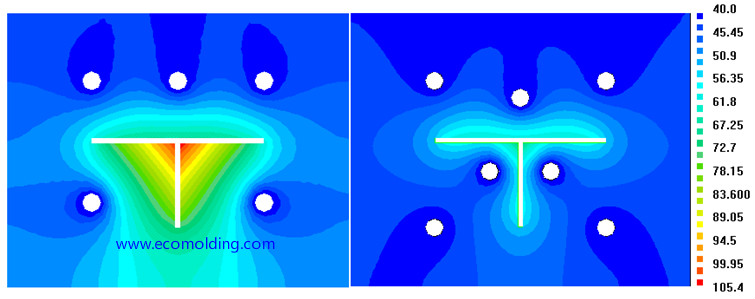
Injection Mold Cooling Channel Size & Layout
The diameter of the cooling channel is preferably greater than 8mm, while the diameter of each tube should be as uniform as possible to avoid pressure loss caused by uneven flow rate of the coolant.
Regardless of the mold size, the diameter of the cooling channel can’t be greater than 14mm, or it will be difficult for the coolant to form a turbulent flow.