The Basic Composition of Injection Mold Cost
The mold is an important process equipment for the manufacturing of various industrial products, so it has become the prerequisite for the development and production of diversified industrial products. However, a mold usually does not directly enter the field of market circulation, but is manufactured on basis of the one-to-one make-to-order contract agreed upon by the supply and demand sides through business negotiation. At the same time, the mold is a technology-intensive product with a small production batch for each mold, so it poses higher requirements for production organization, equipment and HR allocation. How to determine the injection mold price in a timely and reasonable manner is one of the main tasks for reaching a mold processing agreement.
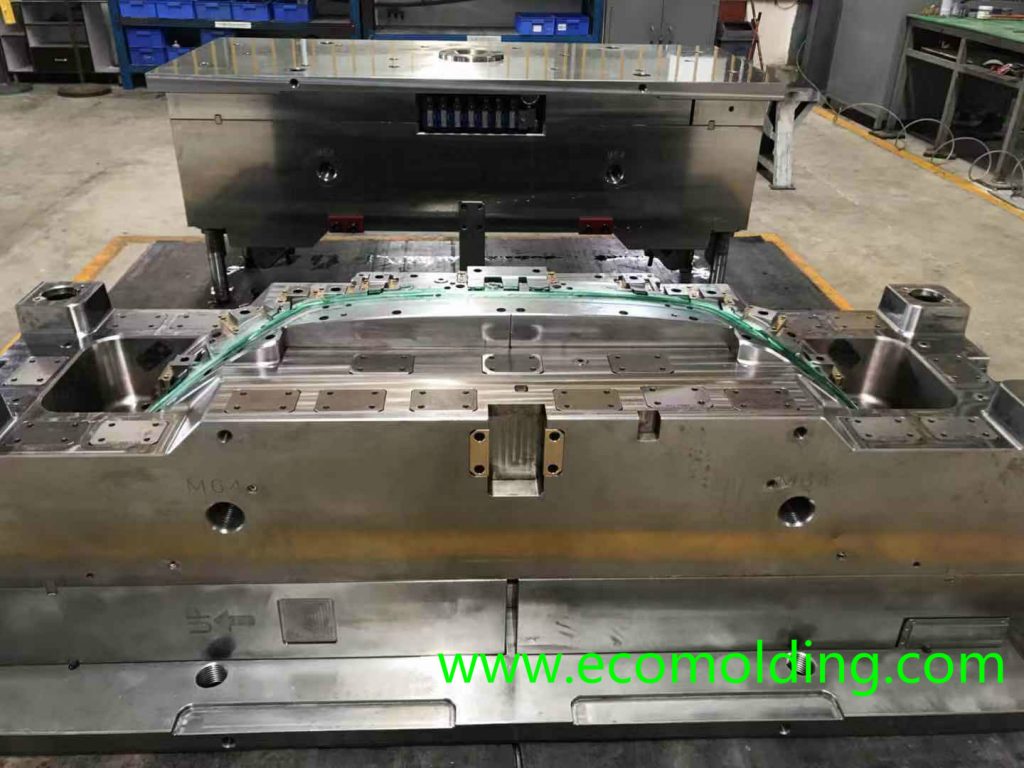
Particularly, the technological value and expedited production cost (i.e., the cost increase caused by shortening the mold making cycle, also known as the crash cost) of a mold product needs to be reflected. Therefore, the price of a mold = material cost + manufacturing cost + overhead cost + profit + tax + technical value ; expedited production cost = mold cost + profit + tax + technical value and crash cost. Among them, mold cost = material cost + manufacturing cost + overhead cost. The manufacturing cost can be considered as the cost incurred by mechanical work, and the overhead cost refers to the various costs and expenses incurred by non-machine tool operators during mold production.
Calculation of Injection Mold Price
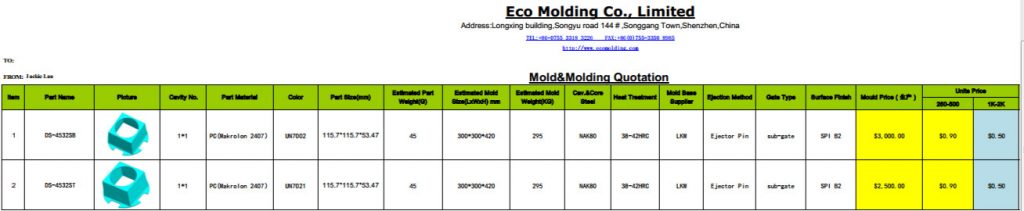
1. Calculation by Experience
Mold price = material fee + design fee + processing fee & profit + VAT + mold trial fee + packaging & transportation fee, and the proportion of each item usually is:
Material fee: the cost of materials and standard parts account for 15%-30% of the total mold cost;
Processing fee & profit: 30%-50%;
Design fee: 10%-15% of the total mold cost;
Mode trial fee: the trial cost of large and medium molds can be kept within 3%, and that of small precision molds within 5%;
Packaging & transportation fee: can be calculated by the actual amount or 3%;
2. Material Coefficient
Mold material fee can be calculated on basis of mold size and material price.
Mold price = (6~10) * material fee
Plastic mold = 6 * material fee
Die casting mold = 10 * material fee
Estimation of Mold Price
1. The first thing is to take the customer’s requirements into consideration, because these requirements determine the choice of material and thermal treatment process.
2. After material selection, develop a rough mold plan from which the weight of the mold (calculating the cost of the core material and formwork material) and the cost of thermal treatment can be calculated. (The weight of the mold base)
3. Processing cost – according to the complexity of the mold core, the ratio between the processing fee and the core material price is generally 1.5-3:1, and the processing fee of mold base is usually 1:1.
4. The cost of risk is 10% of the total price mentioned above.
5. The design fee is 10% of the total mold cost.
Injection Mold Price Estimation and Quotation
The mold is a hi-tech product for a special purpose, as a result we should not cater to customers with low price or even selling at a loss. Instead, we should guarantee high quality and a favorable price, and put the quality, precision and service life of the mold in the first place, without overvaluing the mold cost. If you pursue low prices mold, it will be difficult to guarantee the quality, precision and service life of the mold. In the case that mold manufacturing shares the same accounting unit with product development & production, or is financially interrelated with it, its cost price should be quoted as the mold price. Mold price estimation should only include basic cost price of the mold, leaving aside other costs and the profit for the time being. Subsequently, the added value of the mold fee can be extracted from the profit as compensation after the mold is put into production. However, the quotation at this timepoint cannot be used as the actual price of the mold, but only as mold cost in the early development stage. In the future, once the product is successfully developed and profits are generated, the added value of the mold fee should be extracted and returned to the mold maker. The sum of the two forms the price of the mold. At the moment, the price of the mold may be higher than the one obtained in the first scenario, and even with a very high return rate, which is tens or hundreds of times higher than the original mold cost. Of course, it is also possible that the ROI is 0.