Proper Mold Design
When molding with engineering plastics, such as POM (polyoxymethylene), PA (nylon), PBT and PET (polyester), the correct mold surface temperature plays a very important role. After mold design meets the basic product requirements, the molding operator is only able to produce great quality products with the help of a mold temperature controller.
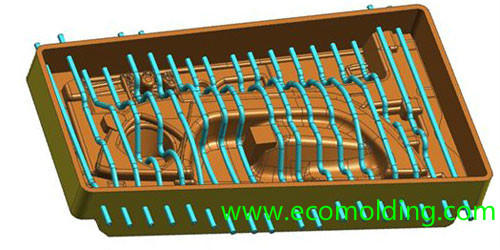
Adverse Impacts Caused by Improper Mold Temperature
1) If the mold surface temperature is too low, poor appearance tends to be caused on molded product, with easily identifiable defects. Also, if the mold surface temperature is too low, dimensional shrinkage of the product will be caused when applied under high temperature conditions. A too-low mold surface temperature causes the mold shrinkage to decrease, but that of the molded product to increase.
2) The shrinkage of an engineering plastic mold, as well as that of the molded product is closely related to mold temperature and the wall thickness of the product. Uneven heat distribution within the mold can lead to different shrinkage rates, resulting in oversized products.
3) If the dimensional stability of a product requires a long cooling time, it means that the temperature control of the mold is not effective. This is caused by the too long time needed for the mold temperature to rise and reach a balance.
4) Uneven heat distribution on the mold surface will extend the molding cycle, resulting in reduced production efficiency and increased molding costs.
Suggestions on Proper Mold Temperature Settings
1) The molds for engineering plastic products are becoming more and more complex, making it harder and harder to set the reasonable and effective mold temperature control. The mold temperature control system needs to be taken seriously for all applications except some simple products.
For proper mold temperature control, please refer to the following suggestions:
Mold temperature control of a molded product must be considered during mold design;Great heat transfer in the mold structure is of great importance when the designed mold has a small injection weight but a large mold size;The flow path of the mold coolant should be smooth. Try not to use quick connectors, which may hinder the flow of mold coolant;When using pressurized water as mold coolant, the hose and the manifold must be able to withstand high pressure and high temperature; Choose the appropriate mold temperature controller, of which the data sheet should indicate the cooling medium and flow rate;Apply a heat insulator between the mold and the cavity plate of the molding machine;Use different temperature control systems for mold core and mold cavity;The cavity and the core of a mold use different temperature control systems, so when the mold runs, different cooling temperatures can be generated;
Different mold temperature control circuits are connected in series, while parallel connection is prohibited. When the circuit is connected in parallel, even the slightest flow resistance will cause difference in the volume flow rate of the coolant, and greater mold temperature variation will be caused when compared with the series circuit (the parallel circuit connected mold can only run properly when the temperature difference between the inlet and the outlet of the mold coolant is kept within than 5 °C); the mold temperature controller needs to have a device for indicating the supply temperature and the return temperature;
2) A mold reaches its thermal balance after multiple injection runs, at least 10 runs under normal conditions. The actual mold temperature at balance depends on many factors.
3) The actual temperature at which the mold surface contacts the plastic can be measured by thermocouples within the mold or more commonly by a handheld thermometer. The surface probe of the thermometer must be able to respond quickly, while the mold temperature needs to be measured at many locations, rather than just one location on each surface. The temperature control system is then modified to adjust the mold temperature to the required level. The recommended mold temperatures, typically provided in the data sheets of a variety of different raw materials, are the optimal mold temperatures to achieve the best surface finish, mechanical properties, shrinkage and cycle times for the molded product.
4) When molding precision, optical and safety parts, it is usually preferred to select a higher mold temperature (allowing the molded part to have a low shrinkage, a smooth surface, and a uniform material); for parts with lower technical requirements, a lower mold temperature is usually selected, so as to minimize the production cost. Pay attention to the defects caused during low-temperature molding, test the strength of the parts, and confirm that they meet the customer specs.