At present, the manufacturing industry uses different plastic molding materials to produce different products. Each part needs a unique plastic forming process, Which can form part, according to the specifications of the parts. Before producing plastic products, you need to determine the most specific plastic forming processes that bested meets your production needs. In this paper, five different types of plastics molding, their advantage and specific application are summarized.
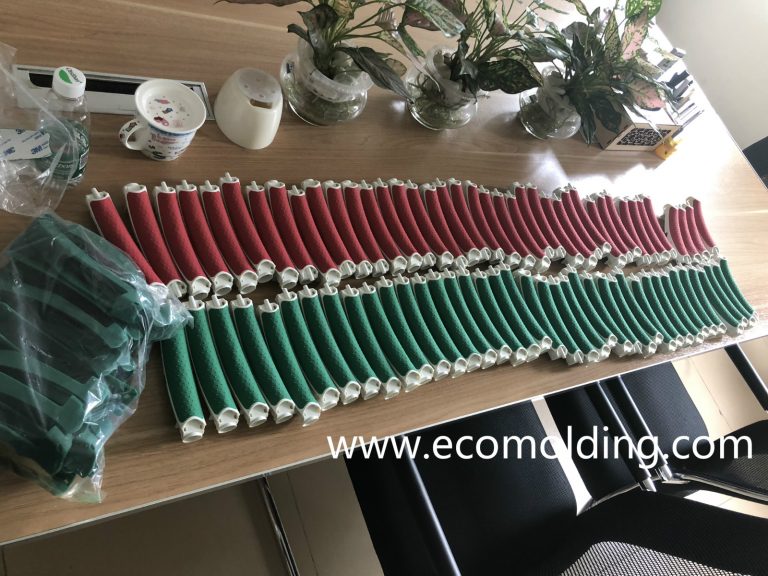
Blow Molding – applicable for production of hollow items, e.g. bottles
Blowing molding is usually used in glass blowing. One of the billets (heat plastic parts, usually a tube) is inflated. The plastic material is push by air onto the die to obtain the desired shape. After cooling, the plastic parts will be ejected.
The forming process mainly use mainly use for mass productions of hollowed products. It’s the right processes for you to make most plastic bottles. Blow molding can produce thin-walled container in a very more consistent and economical way. C
Compression Molding – applicable for production of larger items, e.g. automotive spare parts
As the name implies, in this forming process, the heated plastic material will be placed in a heated die, Which will compress it into the desired shape. Although plastic materials are usually flaky, they can also be bulky. Maintains the integrity of the final product by car (heating). Liked other, forming processes, part will be ejected after forming. In the case of use plastic sheet, the plastic material needs to be repaired in the mold before the part are removed
Compression mold is designed to treat high strength compound such as thermosetting resins, Glass fibers and reinforced plastics. In the compression forming process, the application of materials makes it have excellent strength performance, Which is the much suitable processes for automotive parts production.
Extrusion Molding – applicable for production of long hollow objects, such as tubes, pipes and straws
Different from other molding processes which get the plastic materials into a mold through pressure, extrusion molding, as its name indicates, extrudes the molten plastic into a tooling, instead of a mold, to get the shape of the final product.
The extrusion process forces the molten plastic material to pass through the tooling to obtain the desired shapes with a fixed cross section. Through this process, many different shapes can be obtained effectively. Because plastic materials need to be melted and then solidified, Only thermoplastic have sufficient strengths to carry out extrusions process. After cooling, the final extrude parts can be cut or roll to be packaged and shipment.
Injection Molding – applicable for production of high-quality, high-volume parts
Among all molding types, injection molding serves the most versatile purposes. The injection molds are generally made from steel and designed with cavities to form the part. During this process, molten plastic is injected into the mold, and filled into mold cavities. After cooling, the part will be ejected by ejector pins.
In this method, the cost of the mold itself is high, but the cost of every part is rather low. Cost effective part, diversified resin and finish options have made the injection molding process a popular technique in the present manufacturing industry.
Rotational Molding (AKA Rotomolding) – applicable for production of large, hollow, one-piece items
Rotational molding coats the mold interior to form the desired part by using high temperatures and rotational movements. In this process, the mold rotates constantly to create the centrifugal force that is used to form even-walled parts. Though not a very fast moving process, it is an ideal method for manufacturing of large hollow containers, e.g. tanks. In this very process, little material is wasted and excess material can be recycled, making it not only economical, but also environmentally friendly.
Every plastic molding method has its unique advantages and disadvantages. Designers and engineers need to keep their differences and characteristic in mind when choosing the most appropriate process for product manufacturing. Mold making company should provide more consideration into what is the best process for customer’s project