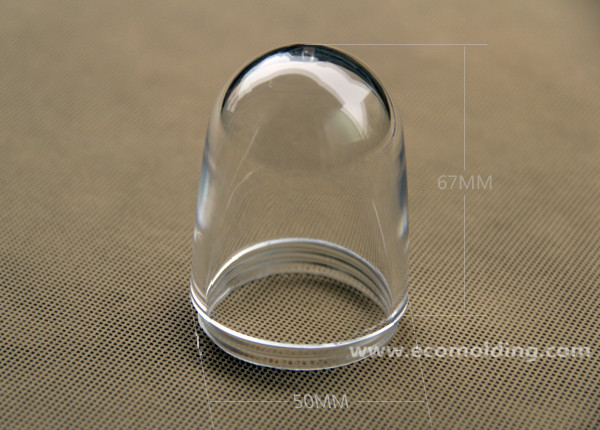
In PC plastic injection molding process, the choice of moisture control and molding conditions are the two most important factors that affect the quality of the molded product, as respectively described below:
Moisture Control:
PC plastics are prone to hydrolysis, bond breaking, molecular weight reduction and physical strength decrease even when they encounter a very low level of moisture. Therefore, before the plastic injection molding process, the moisture content of PC should be strictly controlled below 0.02% to avoid a decrease in the mechanical strength of the molded product or an abnormal appearance, e.g., bubbles, crazes or the like on the surface. In order to avoid abnormalities caused by moisture, the PC should be dried in a hot air dryer for 3 to 5 hours before processing with the temperature set at 120°C, or remove the moisture by a dehumidifier, but the dehumidified air should have a dew point of -30°C at the entrance to the funnel.
Injection Molding:
To satisfy the needs of various injection molding processes, PC materials are designed with different melt flow indexes. Generally speaking, a melt flow index of 5 to 25 g/10min is suitable for the plastic injection molding process. However, the optimal processing conditions vary greatly depending on the type of the injection molding machine, the shape of the molded product, and the specifications of the PC material, so adjustment should be made according to the actual situation.
1. Selection of Injection Molding Machine:
Clamping Force: 0.47 to 0.78 tons per square centimeter (or 3 to 5 tons per square inch) of the projected area of the finished product.
Machine Size: The weight of the finished product measures about 40 to 60% of the capacity of the injection molding machine. If the machine is measured with polystyrene (ounce), it needs to be reduced by 10%. 1 ounce = 28.3 grams.
Screw: The length of the screw should be at least 15 times the diameter, and the optimal length is when L/D = 20:1. The compression ratio preferably ranges from 1.5:1 to 30:1. The stop valve at the front end of the screw should adopt the sliding ring, while the flowable gap of the resin should be at least 3.2mm.
Injection Nozzle: The tip opening should be at least 4.5mm (diameter). If the finished product weighs 5.5kg or more, the nozzle diameter should be 9.5mm or more. In addition, the tip opening needs to be 0.5 to 1mm smaller than the gate diameter, and the shorter the section, the better, about 5mm.
2. PC Injection Molding Conditions:
Melt Temperature & Mold Temperature:
The optimal molding temperature setting is dependent on many factors, such as the size of the injection molding machine, the screw configuration, the design of the mold / molded product, as well as the molding cycle. In general, in order to gradually melt the plastic, a lower temperature is set in the rear/feeding zone of the feeding pipe and a higher temperature in the front section. However, if the screw is not designed properly or the L/D value is too small, a reversed temperature setting is also feasible.
With regard to mold temperature, a high mold temperature ensures a better surface appearance, with a lower residual stress, and also, it is easier to fully fill the thin or long molded product. However, a low mold temperature is able to shorten the molding cycle.
Screw rotation speed: 40 to 70rpm is recommended, but it should be adjusted according to machine and screw design.
Injection pressure: In order to fill the mold as quickly as possible, the higher the injection pressure the better. Usually, the pressure is set at about 850 to 1,400kg/cm2, and the highest can reach up to 2,400kg/cm2.
Back pressure: Generally speaking, the lower the back pressure, the better. But to ensure uniform plastic feeding, 3 to 14kg/cm2 is recommended.
Injection speed: The injection speed has a lot to do with the gate design. When using the direct gate or the edge gate, to prevent flow marks and poor surface finish, a slower injection is applied. In addition, if the thickness of the finished product is above 5mm, in order to avoid bubbles or dents, a slower injection speed can also help. In general, the injection speed is fast for thin products, and slow for thick ones.
Switch from injection pressure to holding pressure: Keep the holding pressure as low as possible to avoid residual stress in the molded product. The residual stress can be removed or reduced by annealing, of which, the condition is 120 to 130°C for about 30 minutes to an hour.
3. Barrel Cleaning:
(1) Add the cleaning material (general-grade polystyrene or benzene) at the molding temperature of PC, and perform twenty to thirty shots;
(2) Retreat the molding machine, and continue inject the cleaning material until the injected cleaning material begins to expand and foam;
(3) Reset the barrel temperature to 200-230 °C; (4) Continue to inject the cleaning material until its temperature reaches 260°C and the appearance looks very clean
Please feel freely to contact us if you are looking for professional plastic injection molding factory