Introduction:
When designing a plastic injection mold, the selection of the parting surface is an important design factor. With a reasonable parting surface selection, the mold structure can be simpler, making it easier to mold and release the plastic product, with product quality guaranteed. If the parting surface is inappropriately selected, mold structure becomes complex, making it difficult to mold the plastic product, thus affecting product quality. Therefore, the selection of the parting surface is of great importance to the design of mold structure.
Definition of Parting Surface
Designed for the removal of the plastic product and the cold slug, the parting surface is where the core meets the cavity, and usually locates at the largest section of a product.
Forms of Parting Surface
1.Flat Parting Surface (See Fig. a)
2.Angled Parting Surface (See Fig. b)
3.Stepped Parting Surface (See Fig. c)
4.Curved Parting Surface (See Fig. d)
Please see the following figures:

Design Principles of Parting Surface
1,The parting surface should be located at the largest section a plastic part
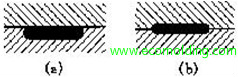
b is appropriate, because the parting surface is designed at the maximum section of the product, able to ensure smooth mold release
2.The selection of the parting surface should be helpful for mold release / product ejection
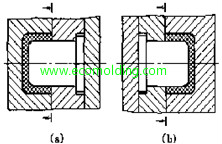
b is appropriate, because the parting surface is designed on the movable mold half. After the mold opens, the plastic product wraps around the core of the movable mold half due to shrinkage, while the ejection system is generally designed on the movable mold half, so it is easier to release the mold
3.The parting surface should be selected to meet the appearance requirements of the plastic product
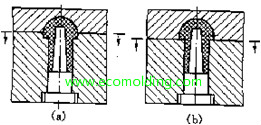
a is inappropriate, because it is easy to cause flash or steps, affecting the appearance of the plastic product, so b is more appropriate.
4.The selection of the parting surface should ensure the precision requirements of the plastic product
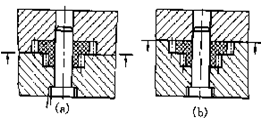
a is inappropriate, because this does not guarantee the coaxiality requirements of the double plastic gears. Usually the part with coaxiality requirement should be designed in the same side. The solution shown in (Fig. b) is more appropriate.
5.The selection of the parting surface should facilitate mold making
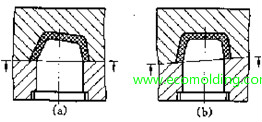
a is inappropriate, because this type of parting surface makes it difficult to process the core, while the solution shown in Figure (b) is more appropriate.
6.The selection of the parting surface should be helpful for mold venting
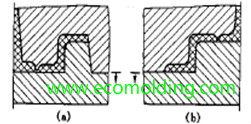
a is inappropriate, because the melt front does not fit the parting surface. It will cause poor venting, and therefore air trapping and burning of the plastic product; Figure (b) is more appropriate.
Please feel freely to contact us if you are looking for a professional plastic injection molding company.