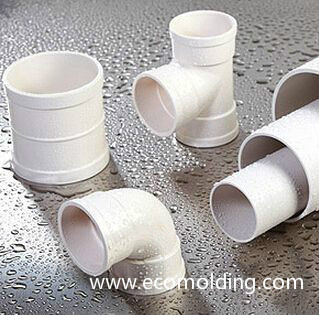
Thanks to its low price, inherently anti-inflammatory features, great hardness and rigidity, as well as the outstanding resistance to chemicals and the shrinkage as low as 0.2-0.6%, PVC products are widely used in electrical appliances, machinery, construction, daily necessities, toys and packaging. Based on the characteristics of the PVC material, its injection molding process is analyzed as follows:
The Characteristics of the PVC Material
PVC is a material that features poor thermal stability, PVC plastic injection molding temperature is close to the decomposition temperature, unfavorable fluidity, as well as an appearance that is prone to defects. Due to its low thermal resistance, it is the easy for PVC to burn, of which the acid gas caused tends to erode the mold. During the plastic injection process, plasticizer can be added to improve its fluidity. Generally, additives are needed to ensure the outstanding strength, electrical insulation and chemical resistance of the material.
Mold & Gate Design
In order to shorten the molding cycle, the gate length shall be minimized, with a circular cross-section design, while the diameter of the injection nozzle is at least 6mm, designed into a cone that has an interior angle of 5 degrees. It is better if a cold slug wells is equipped to prevent the poorly melted semi-solid material from entering the mold cavity, which might affect the surface finish and the strength of the product.
The draft angle should be designed between 0.50 and 10 degrees to ensure that there are sufficient venting mechanisms in the cavity. The common vent size is 0.03-0.05mm deep and 6mm wide, or allow a 0.03-0.05mm gap between each ejector pin. The mold is made of stainless steel or is hard chrome plated.
The PVC plastic injection molding Process
PVC is a heat-sensitive plastic material. Excessive heat or excessive shearing will cause decomposition that spreads quickly, because one of the decomposition products (such as acid or HCI) will cause catalysis, leading to further decomposition of the material, while the acidic substance will corrode the metal, causing dents, peeling off the protective layer, leading to rust and thus making it more harmful to the human body.
The commonly used screw length to diameter ratio ranges from 18 to 24:1, the ratio between the three sections is 3:5:2, and the compression ratio is 1.8 to 2. The recommended thread depth of the feed section is as follows:
Screw diameter (mm): 35 / 50 / 60 / 75 / 100
Thread depth (mm): 2 /3 / 4 / 5 / 6
The tip of the screw should have an interior angle of 25 to 30 degrees. When the screw is in the full injection position, the distance between the tip and the nozzle should be 0.7 to 1.8 mm. The screw must be made of stainless steel or chrome plated.
1) Screw cushion: The screw cushion is between 2 and 3mm, or higher for large machines.
2) Injection volume: The actual barrel residence time cannot exceed 3 minutes.
3) Barrel temperature setting:
The temperature provided here are only for reference. It should be properly adjusted according to the actual conditions of the machine and the raw material, and may sometimes exceed the recommended range.
Position: Mold / Nozzle / Front Section / Mid Section / Feed Section
Temperature (°C): 30-60 / 170-190 / 160-180 / 150-170 / 140-160
The injection volume applied is 20-85% of the theoretical injection volume of the injection molding machine. The lower the actual injection volume, the longer the residence time of the material, and the greater the risk of degradation after being heated.
4)Barrel Residence Time
Under 2000 °C temperature conditions, the barrel residence time (of the plastic material) can be more than 5 minutes.
5) Injection speed:
The injection speed should be slow, otherwise excessive shearing will degrade the material. When UPVC is used to produce extremely smooth thick-walled products, multi-stage injection speed should be applied. If light brown stripes leak out from the gate, the injection speed would be too fast.
6) Back pressure: The commonly used surface value is 5 bar. Though increasing the back pressure is helpful for color mixing and venting, the back pressure should be kept as low as possible.
7) Shutdown: Due to the low thermal stability of PVC, the shutdown part is very important. The barrel should be cleaned by using other thermoplastics with high thermal stability and non-resistance to PVC (such as PMMA, PP, LDPE, or GPPS). Don’t mix POMT and UPVC in the same barrel, or it will lead to excessive chemical reaction and cause serious damage to the machine.
8) Mixing ratio: The maximum mixing ratio of degraded material is 20%, or product quality will be affected.
9) Typical products: The main application of UPVC is to produce drainage pipes, or computer / television casing, water filter groove, photocopying machine casing, electric and gas meter casing, transparent cover of printing machine, air grating and various electronic parts.
Please feel freely to contact us if you are looking for a professional plastic molding company.