(1) What is bubble (appearance)?
Bubble refers to the phenomenon in which the surface of a molded product bulges.
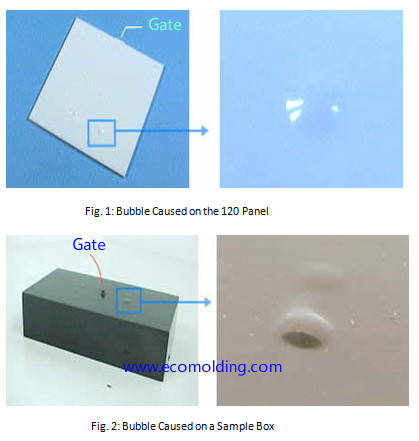
Bubbles are prone to occur in the following two scenarios, i.e., the surface of the product gradually starts to bulge when it is taken out of the mold after plastic injection molding, and the surface of the molded product bulges due to thermal expansion. In either scenarios, when the surface of the molded product becomes soft due to high temperature, the internal air is heated up to cause the surface of the molded product to rise, thereby creating a bubble.
(2) Causes of Bubbles
(2-1) Trapped Air
If a large amount of air is involved in the metering process, it is easy to generate a bubble. Specifically, it is easy to cause a bubble when the screw speed is fast, the back pressure is low, and the injection volume is large. In addition, during the cavity filling process, some flow patterns sometimes also cause air to be trapped in, creating a bubble.
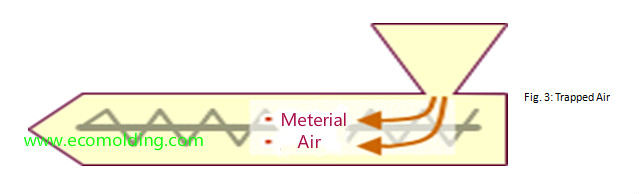
(2-2) A large amount of gas is generated in the resin
The bubble is also easily caused by a large amount of gas generated in the resin. When the temperature of the barrel is too high and the residence time is too long, the generated gas will increase, and the bubble is thus easily generated. In addition, when there is insufficient drying and too much moisture is contained in the material, the bubble is also generated.
(3) Solutions for Bubbles
(3-1) Reduce trapped air
To reduce trapped air during metering, the following conditions should be changed:
· Reduce the screw speed
· Increase the back pressure
· Do not set the injection volume too high
If air is trapped during the mold cavity filling process, the shape, gate position, and injection speed need to be adjusted. This should be specifically dealt with according to the condition of the molded product. Through the short shot, understand the flow pattern, and then establish corresponding countermeasures based on this.
•(3-2) It is difficult to peel off the layers
Changing the holding pressure has no effect on improving the bubble. It is better to reduce the shear force during filling so that the material can smoothly fill the cavity to be more effective in eliminating the bubble. Specifically, the following molding conditions can be changed:
· Increase the mold temperature
· Lower the injection speed
· Enlarge the gate
· Increase the thickness (only for the too thin part)
· Avoid jetting
(3-3) Control gas generation
· Improve drying, remove low-molecular polymer (oligomer) in the resin while removing moisture.
· Lower barrel temperature (within the recommended temperature range rather than excessively)