(1) What Is Burn Mark? (Appearance)
Burn Marks refers to the blackened edge that is caused on the surface of a molded product during the injection molding process.
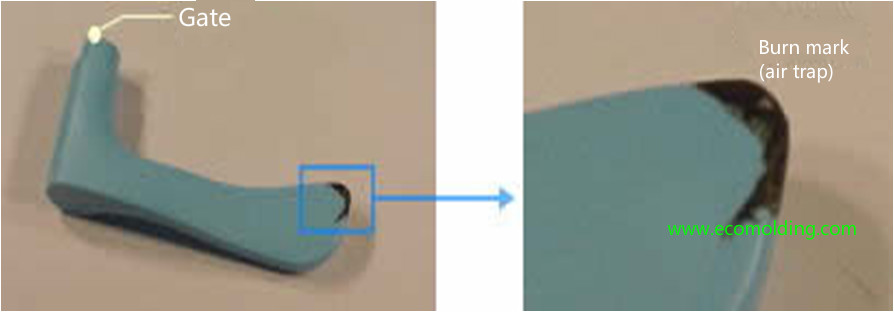
When the resin is filling the cavity, the original air is discharged through the vents. At this time, the gas generated by the resin is also discharged from the vents. However, if the vents of the mold are clogged, or there are no vents at the end of the flow, the gas will not be fully discharged, which, after being compressed, creates a high temperature, causing the resin to be burnt.
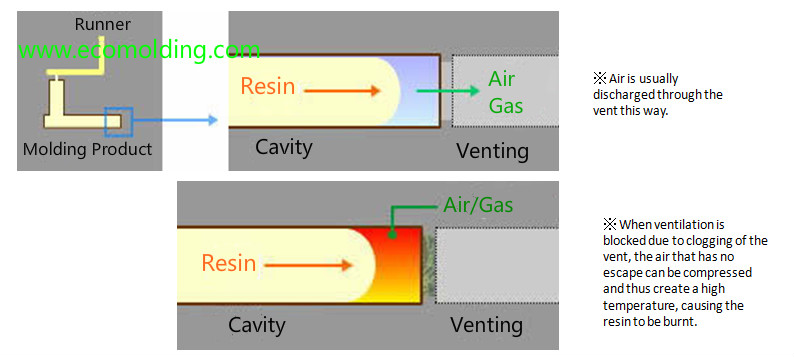
(2) The Cause of Burn Marks
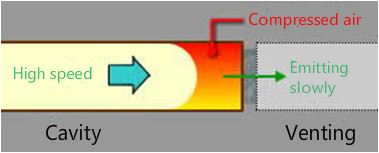
(2-1) When the injection speed is fast, with the filling of the resin, the air in the cavity and the gas contained in the resin are discharged through the vent. However, if the injection speed is too fast, there would be not enough time for the gas to be discharged from the vent, but will be heated by insulated compression, thus creating a high temperature, which leads to the burn marks. When VP switching is slow, it is also very easy to cause burn marks for the same reason.
(2-2) Poor Ventilation
Similar to the above scenario, burn marks also occur when the ventilation capacity of the vent is low. There are two reasons: one is that the thickness of the vent is originally thin, and the other is that the vent is blocked by the mold deposit during application. Due to the same reason, when there is too much gas contained in the resin, the burn marks will worsen.
(2-3) Too-high Mold or Resin Temperature
When the mold temperature or resin temperature is too high (although it is only a secondary reason), burn marks also tend to worsen.
(3) Solution for Burn Mark
(3-1) Slow Down the Injection Speed
Burn Marks are caused by the gas being rapidly compressed to form a high temperature. Therefore, slowing down the injection speed is able to reduce burn marks. When the shape of the molded product is limited, adjust the VP switching position or employ multiple-stage injection. If the problem cannot be solved anyway, such measures as optimizing the vents should be applied to improve the ventilation.
(3-2) Improve Ventilation
For the vent, please check the following items:
· Is it blocked by mold deposit?
If it is clogged, please clean it up. Vents with poor performance are prone to blockage.
·Enhance the ability of the Vent
Increase the quantity and thickness.
· Is it appropriately placed?
If there’s none at the flow end, it will be meaningless.
Please design the vent effectively at the point where the burn marks occur.
•※ After implementing these countermeasures, other failures may occur. Therefore, do not over-change the settings. Please take a note of this.
Please feel free to contact us if you are looking for a professional injection molding company