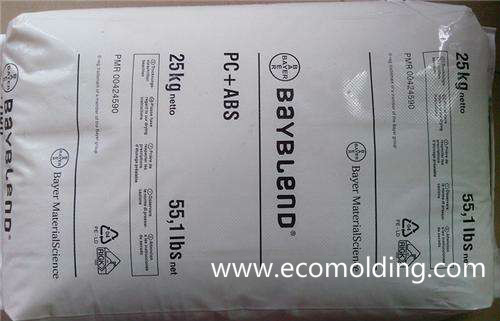
What is the PC+ABS material? What are the purposes of PC+ABS? And, what is the injection molding process of it?
PC plastic is a new type of thermoplastic with a transparency of 90%, and is thus dubbed a transparent metal. It is rigid and tough, possesses high impact strength and high dimensional stability, as well as a wide range of application temperatures, great electrical insulation, heat resistance and non-toxicity properties. ABS, a tough and rigid thermoplastic, is a blend or terpolymer of acrylonitrile, butadiene and styrene. Styrene gives ABS great moldability, gloss and rigidity; acrylonitrile gives ABS great resistance to heat and chemicals, and outstanding surface hardness; butadiene gives ABS great impact strength and low-temperature resilience.
PC+ABS is a thermoplastic made of PC and ABS alloys, which combines the excellent properties of both materials. It is widely used in automotive trims, lampshades, handles and other components; consumer and commercial appliances, such as computers, peripherals and mobile phones; able to replace PC for production of thin-walled products and those with long flow paths as well; camera components, instrument panel, fan cover, hard hat housing, screw cap, radiator grille, computer and optical instrument housing, hair dryer and coffee maker, etc.
The countries producing PC/ABS include SABIC Innovative Plastics, Bayer (Germany), Chi Mei (Taiwan, China), Teijin (Japan), LNP (the US), LG (South Korea), Mitsubishi Engineering (Japan), and Cheil Industries of Samsung (South Korea). The specific models include:
HC1204HF,C6200-111,NX07343 BKID749,NX07344 BK1E257,NX07344 BK1E5
65L,XCY620H,XLY620,C2801,C2801-BL3230,C6802-HT001BK,C7210A,C2950-76701,CM6140-BK1C288,CX7240-BL,LG8002,LG9000,LG8002-100,LG9000-BR5097,C2950-1001,C7230P,Z48-BK,NX07331,NS0031 GY6D264,NL001WH8E117,MC8800 BK1005,MC8002-701,MC8002-100,MC1300-100,EXCY0279BK,CX7240 BK,CX7240-111,CX7240 BK1A382,8002,C1200HF-100,C2100HF WH,C2100HF-111,C2800,C2951-WH4052
Germany Bayer:T45PG,T65 900812,T-85 500069,FR2000,FR2010,FR3000,FR3005HF 901510,FR3002 BK,FR7000,T-85-702332,T85MN,T88 GF20,T88GF20 901510,T88 GF20 BK,FR110-901510,FR3002,FR90,T-65-901510,FR86,1518B,T85 XF
Taiwan Chimei:HF-420,PC-365,PC-385,PC-510
Japan Panlite:7800-BK,DN-1825B,RH-3130 BK,TN-3000V,TN-7100F,TN-7700 BK,RN-3120,T-3713,TE-3414Q-VO,T-105 PC/ABS
USA LNP:EXP2SL,FXC810ME,NS0031,NS0031 BK2D038,NX07344 BK1E257,NX07354 BK,NX10302 BK,PCAB1004 BK82075,PCAS1002,PCA-S-1002 FR NAT,PCAS1003FR,PCAS1003,PCAF1006,OFRECO2EXP2-SK
Korean LG:HR-5007A,SG-5009F,GP-5008B,LT1B-EF56,HP-5004 KA02Z,GP-5300,GP-5200,GP-5106F,GP5008BF,GN-5008A
Janpan Mitsubishi:PC/ABS:MB-1800 BK30,MB1801E BK30,FM1220,PM2211 NC,MB2215R
Korean Samsung:EN-1052,HI-1001B,HI-1001BN,HI-1001BN-K2261,HI-1001BNW91605,LS-1150G,1015L,HP-1000P,NH-1017D,ST-1009
The Characteristics of PC+ABS:
• Great overall performance, high impact strength, chemical stability and outstanding electrical properties.
• Great weldability with plexiglass, allowing for production of two-color plastic products, able to be chrome-plated and painted.
• Various grades available (by impact, thermal resistance, flame retardancy, enhancement, transparency and more).
• The fluidity is a little lower than that of HIPS, but better than that of PMMA and PC, with desired flexibility.
The plastic injection process of PC+ABS:
Drying: Drying before processing is a must to keep the humidity below 0.04%. The recommended drying condition is 90°C-110°C for 2-4 hours;
Barrel Temperature: feeding section – 50-70°C (70°C);
Melt Temperature: 230-300°C;
Constant Barrel Temperature: 200°C;
Mold Temperature: 70-90°C;
Injection Pressure: 80-150MPa (800-1500bar);
Holding Pressure: 40%-50% of the injection pressure, so as to avoid product shrinkage; to minimize product internal stress, the back pressure should be set as low as possible, i.e., 5-10MPa (50-100bar), in order to prevent frictional heat.
Injection Speed: Apply a medium injection speed to minimize frictional heat; multi-stage injection; slow-to-fast injection is recommended for some products;
Screw Speed: Maximum screw speed equals linear velocity at 4.0m/s;
Screw Back Position: (1.0 to 3.0) D, because the melt is sensitive to overheating and excessive residence time in the barrel;
The residence time should not exceed 6 minutes, and the residence time in the hot runner should be as short as possible. The amount of cushion is 2 to 5mm, depending on the screw back position.