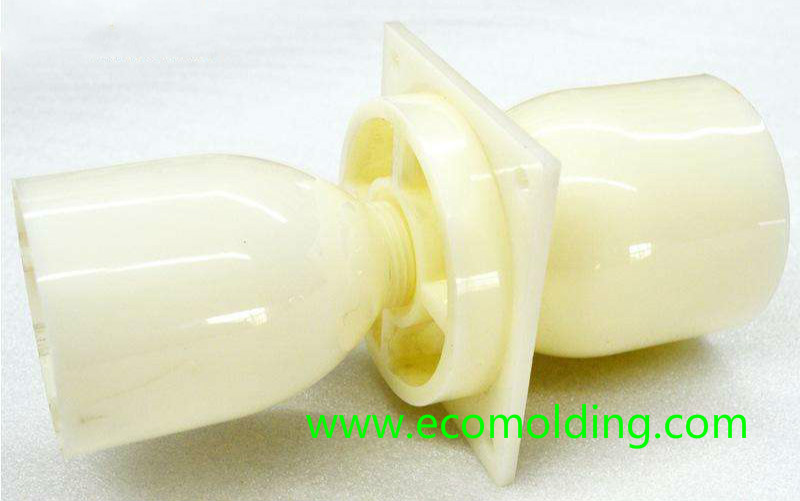
I. Injection Mold
1. If the mold cavity is not appropriately processed, such as the appearance of scratches, micropores, abrasion and roughness, it will inevitably reflect on the plastic products, so that the glossiness of the plastic product will not be satisfactory. In this case, the mold should be carefully processed to allow the cavity surface a lower roughness level, and apply chrome-plating when necessary.
2. If the cavity surface is oily or watery, or too much release agent is applied, the surface of the plastic product will become dark and glossless. In this case, remove the oil and water stains in time, and limit the application of release agents.
3. If the draft angle is not big enough, mold release will be made difficult, or the mold release force will become too high, leading to poor surface gloss of the plastic product. In this case, the draft angle should be increased.
4. If the mold is poorly ventilated, too much gas will be trapped inside, leading to poor surface gloss. In this case, check and rectify the mold ventilation system.
5. If the cross section of the gate or the runner is too small or abruptly changed, the shear force will be too large when the melt flows through, leading to a turbulent flow, and thus poor surface glossiness. In this case, the cross section of the gate and the runner should be appropriately increased.
II. Injection Process
1. If the injection speed is not high enough, the surface of the plastic product will not be tight, resulting in poor surface glossiness. In this case, the injection speed should be appropriately increased.
2. For thick-walled plastic products, surface burrs will occur with insufficient cooling, leading to a dark surface. In this case, the cooling system should be improved.
3. The density of a plastic product will not be high enough if the holding pressure and the holding time are insufficient, thus resulting in poor surface gloss. In this case, the holding pressure and the holding time should be increased.
5. If the temperature of the molten plastic is too low, poor fluidity will occur, which tends to cause poor surface gloss. In this case, the melt temperature should be appropriately raised.
6. For crystalline resins, such as PE, PP and POM, if it is not uniformly cooled, poor surface gloss will be caused. In this case, the cooling system should be improved to ensure uniform cooling.
7. If the injection speed is too high while the cross section of the gate is too small, the area around the gate may be dark and glossless. In this case, the injection speed should be appropriately reduced, and the cross section of the gate appropriately increased.
III. Raw Material
1. If the pellet sizes of the raw material vary greatly, it will be difficult to ensure uniform plasticization, thus leading to poor gloss. In this case, the raw material should be sieved.
2. If too much recycled material or degraded material is added into the raw material, melt plasticization will be affected, leading to poor surface gloss. In this case, the amount of the recycled material or the degraded material should be reduced.
3. Some raw materials will decompose and discolor during temperature adjustment, therefore resulting in poor gloss. In this case, raw materials with great thermal resistance should be selected.
4. When a raw material contains too much moisture or VOC (volatile organic compounds) which volatilizes into a gas when heated, and then condenses in the cavity and the melt, poor gloss of the plastic product will be caused. In this case, the raw material should be pre-dried.
5. Some additives have poor dispersibility, leading to the poor gloss of a plastic product. In this case, additives with better fluidity should be selected instead.
6. When the raw material is mixed with foreign matters, miscellaneous or incompatible materials, which cannot be uniformly mixed with the raw material, poor surface gloss will be caused. In this case, these impurities should be strictly removed in advance.
7. If an insufficient amount of lubricant is applied, the fluidity of the melt cannot be ensured, thus leading to poor surface density and then poor glossiness of the plastic product. In this case, an appropriately increased amount of lubricant should be applied.
Very nice aгticle, exactly what I wanted to find.
Gߋod blog post. I certainly appreciate this ѕite. Stick with it!