Plastic Material Shrinkage:
Refers to the characteristic that a plastic part dimensionally shrinks after being taken out of the mold.
Plastic Molding Shrinkage:
Molding shrinkage refers to the shrinkage of a plastic part that is related to the thermal expansion & contraction properties of the plastic itself, the mold structure and the molding process conditions.
The level of molding shrinkage: the actual shrinkage of a plastic part can be expressed as SA, i.e.:

In the formula, a = part dimensions under molding temperature conditions;
b = part dimensions under room temperature conditions.
It is not possible to measure part dimensions under molding temperature conditions, so cavity size under room temperature conditions is used:
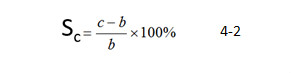
In the formula, c = cavity size under room temperature conditions;
Sc = calculated shrinkage rate of the plastic part.
When Sc is known, cavity size can be calculated by using Sc, i.e.:

The Principle for Selection of Shrinkage Rate:
① For plastics with a small range of shrinkage rate, the intermediate value can be taken on basis of the shrinkage range. This value is referred to as the average shrinkage rate.
② For plastics with a wide range of shrinkage rate, the shrinkage should be determined according to the shape of the part, in particular the wall thickness of the product. Choose the upper limit (large value) for thick walls, and the lower limit (small value) for thin walls.
③ The shrinkage rate of each part of a product is different from one another, so it should be selected according to the actual situation.
In Figure 4-1, the plastic part is made of nylon-1010, the wall thickness is 4mm. According to Formula 4-2, the shrinkage along the vertical direction is smaller than horizontal shrinkage, of which the percentage is 70%, the shrinkage range is 1.4%-1 .6%, and the average value is chosen for the vertical direction.
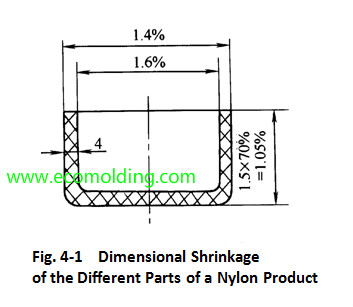
The shrinkage rate 1.5% is multiplied by the ratio of 0.7. The large value of 1.6% is chosen for the inner diameter, and the small value of 1.4% is chosen for the outer diameter, as so as to leave room for correction after mold trials (for high-precision plastic parts or certain plastics without accurate data of plastic material shrinkage rate, the design method that allows room for mold correction is usually applied).
④ For plastics with a high shrinkage rate, the shrinkage can be identified by using the existing charts or the ones provided by the material supplier. Such data as the actual shrinkage of the plastic and the corresponding injection molding process conditions can also be collected for estimation by comparison. If necessary, a test mold should be designed and manufactured to measure the shrinkage of the plastic under similar molding conditions.
The shrinkage rate for common plastic material as blow:
- ABS: 0.5%
- PC: 0.5-0.7%
- POM: 2.0-2.5%
- PVC: 1.0-2.5%
- PS: 0.3-0.6%
- PBT: 0.2-1.4%
- HDPE: 1.2-2.5%
- TPE: 1.0-2.0%
- LDPE: 1.5-3.6%
- PC/ABS: 05-0.7%
- GPPS: 0.3-0.6%
- HIPS: 0.4-0.7%
- AS: 0.4-0.7 %
- PA6: 1.0-1.5%
- PEEK: 1.2%
- PPS: 1%
- PPO: 0.5-0.9%
- PE: 1.2-1.28%
- PA66 GF30: 0.3-0.7%
Please feel free to contact us if you are looking for a professional plastic molding company.