(1) What is discoloration defects (appearance)?
Discoloration means that the color of the molded product is not consistent with the required color.
Since plastic is a chemical substance, it gradually decomposes and deteriorates when it is heated to over the melting point. Discoloration is caused during this process.
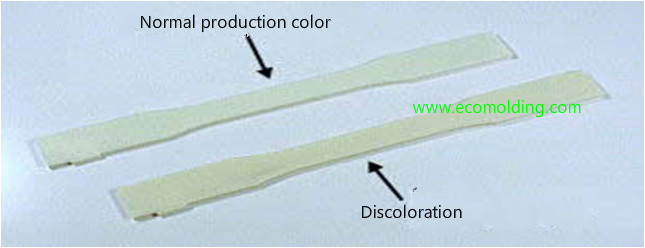
(2) Causes of Discoloration defects
(2-1) Thermal Discoloration in the Barrel
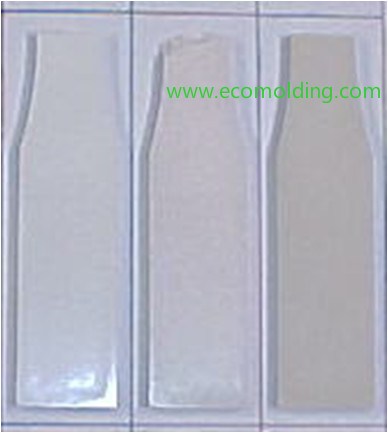
The resin that has melted inside the barrel is often in a high temperature condition. The higher the set temperature, the longer the residence time, and the more the discoloration. In addition, the shear force applied during metering is also one of the reasons for discoloration. The higher the screw speed, the greater the shear force, and the easier the discoloration.
(2-2) Discoloration inside the mold
When the injection speed is too fast, the shear force inside the mold also increases. When the gate or the nozzle is too small, the shear force sometimes increases and thus causes discoloration.
(3) Solutions for Discoloration defects
(3-1) Lower the resin temperature
To prevent resin discoloration in the barrel, lower the resin temperature (including the nozzle) and shorten the residence time.
※ Please also refer to the recommended molding conditions to avoid unreasonable molding conditions.
(3-2) Reduce the shear force during metering
If discoloration occurs during metering, the screw speed should be reduced.
(3-3) Reduce the shear force in the mold
If discoloration defects occurs in a specific part of the mold, such as the nozzle or the gate, the injection speed should be reduced. It is recommended to use multi-stage injection at this time.